Quality is built, not added later
Skilled engineers support the project from start to finish
We choose the best materials and methods to meet or exceed customer needs
Advanced tools help us deliver high-quality, cost-effective results
We use a strong APQP system during development to spot and fix issues early
Cutting-edge simulation tools model mold filling and solidification
Virtual casting helps us improve the design and avoid defects
Quality is checked at every step: during, after, and before shipping
Each workstation is fully equipped to support top-quality casting and machining
Our process ensures defects are caught before moving to the next stage
CAD systems & Simulation
Solidedge CAD
NX CAM
Magmasoft (outsource)
ERP & Data Format support.
Tally Prime.
PDF, STEP, IGES, DXF, DWG, PARASOLID
Foundry Capabilities
Green Sand moulding process with 2 Simultaneous jolt squeeze lines
Inductotherm furnace with 4800 tonne annual capacity
Fully equipped Sand testing laboratory
Metal Analyzer-SPECTRO Germany
Microscope Image Analyzer
Density Index Analyzer
Casting weight - 500 gms to 100 kgs single piece
Core Shooter machines
Physical properties
BHN 3000 kgf testing machine
Rockwell & Vicker's machine
Tensile testing
NDT testing.
MPI testing.
Machineshop Measuring
Faroarm CMM.
3D scanner
Mitutoyo surface roughness tester
All Calibrated conventional testing equipments.
1 mtr x 1mtr surface table
Specialized Gauges for high production
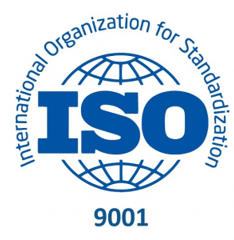
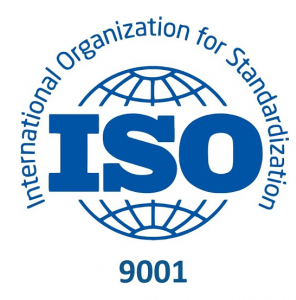
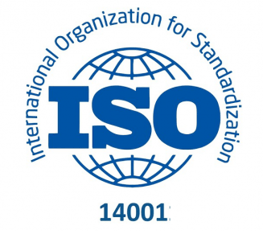
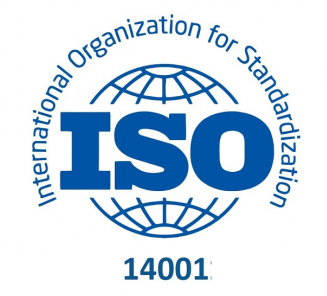
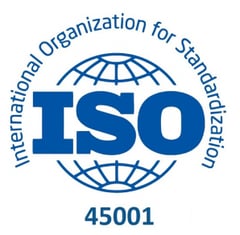
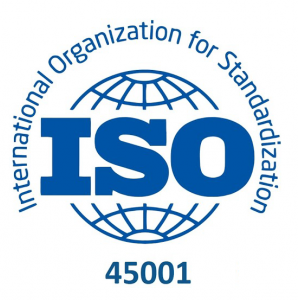
Machine Shop capabilities
CNC turning center
VMC machine
VTL machine
4th Axis rotary
Dynamic Balancing machines
Surface Grinders.
Robodrill
Conventional Machines
MNTR
Toolroom machines